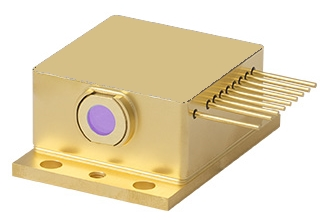
Additive manufacturing, or as its more commonly referred – 3D printing, has revolutionized manufacturing processes over the past ten years. This technology which was once reserved for high-end research and prototyping applications is now so commonplace that many elementary and middle schools through the US are utilizing them as part of their STEM curriculums. The cost of low-end 3D printers has come down so much that, there are now home use “hobbyist” 3D printers available for less than $200. Regardless of cost or complexity, all additive manufacturing processes consist of four primary stages: 3D modeling, digital data processing, 3D object construction, and post-processing. For this blog post, we are going to focus the discussion solely on the 3D object construction phase. During this phase, energy is transferred to a material at a precise location to melt, soften, or cure it enabling layer-by-layer deposition. 3D object construction via this additive process offers several advantages over traditional subtractive manufacturing, including faster construction speeds, less material used, and the ability to manufacture lightweight hollow objects with complex internal structures.
Under the umbrella of 3D printing there is a wide range of methods used for 3D object construction including but not limited to photopolymerization, material extrusion, powder bed fusion, and directed energy deposition. For low-cost applications and material extrusion in general, the preferred methodology is when a nozzle is heated by conduction, enabling the material to flow through the nozzle to the target location. Unfortunately, this process is relatively slow and low resolution compared to other methodologies. For higher speed and high-resolution 3D printing applications, laser-based is preferred because the beam can be efficiently absorbed without any transfer medium. Once the laser is absorbed by the material it can either cause, a photochemical reaction curing the material instantly or photothermal response locally melting and fusing the material; typically, photothermal laser processing is used when 3D printing with metals and powders which sinter or melt when exposed to high power infrared lasers. While metals and powders are being utilized more and more in 3D printing, the vast majority of systems are still polymer based, and for that reason, in this blog post, we will primarily focus on photochemical curing.
The most common photochemical 3D printing method is a process known as stereolithography, which was patented in 1984 by Chuck Hull. In this process, an ultraviolet laser is focused into a vat of photosensitive polymer resin as the beam follows the predetermined path based on the 3D modeling. Once the layer of resin is cured, it is lowered into the vat so the next layer can be cured on top of it. This process is then repeated over and over again until the 3D structure is completed. For the curing process of the photosensitive resin to take place the laser exposure must be above a threshold known as the critical laser exposure. For most commercially available resins used in 3D printing this value tends to fall between 4.3 mJ/cm2 and 7.6 mJ/cm2. Therefore, the higher the laser power and the smaller the spot size, the faster the resin can be cured and the faster the object can be printed.
Traditionally excimer lasers or frequency tripled Nd: YAG has been used for stereolithography, but as laser diode technology has advanced there are now single emitter diodes available which are ideally suited for 3D printing applications. Here at RPMC, we offer a CW 375nm single emitter diode laser from Akela Laser Corporation, with 300mW of output power in an HHL package. the output of a single emitter multi-mode laser diode can be focused down to a spot size of approximately 100 microns in diameter which would result in a curing time between 1 and 2 microseconds for conventional polymer resins. In addition to high speed curing, laser diodes also offer several advantages for integration into 3D printers, including their compact form factor, lower power consumption and long lifetime.
RPMC Lasers is proud to be the North American distributor for Akela Laser. If you would like to get additional technical specifications on the ultraviolet laser diodes pulsed fiber lasers from Akela, click here or talk to one of our laser experts today click here or call 1-636-272-7227.