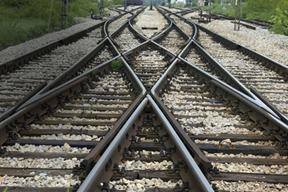
Laser line generators are widely used in machine vision for a broad variety of inspection applications.   When used for the inspection of small parts laser lines and other shapes are typically achieved through the use of diffractive optical elements to create a wide variety of geometric shapes and patterns, but diffractive beam shaping requires the use of single-mode diode lasers.   As the objects under inspection grow in size so do the demands on the size of the laser lines, and there quickly comes a point at which the laser power outpaces what is available from commercial single-mode laser diodes.   As a result, in order to generate large lines from higher powered multi-mode lasers diodes either galvanometric scanning mirrors or micro-optic arrays are required. While scanning mirrors can be rather effective at producing uniform laser lines, they suffer from reliability issues especially in rugged environments making them a less than ideal solution for field deployable systems.  Micro-lens arrays, on the contrary, are a monolithic solution with can either be placed at the output of a bundle of fiber-optic cables or directly in front of the diode bar exploit inherent astigmatism, to produce flat top laser lines.
These high-power laser lines, produced using micro-optic arrays, can be used at distances up to 3 meters from the source with fan angles as large as 110-degrees, making them ideal for inspecting larger objects and surfaces. In the figures below, you can see an example of the laser line cross-sections for a FocusFlux EL series line laser system from Focuslight measured at a distance of 2 meters from the source.
To demonstrate the usefulness of such a laser system, we can take a look at the application of machine vision in the transportation industry for laser rail inspection where high-power laser diodes are widely deployed. These laser rail inspection systems use high-speed cameras in conjunction with high power laser line projectors mounted on rail vehicles to acquire high-resolution digital images and 3D profiles of the rails and beds.  This data can then be feed into specialized image processing software to automatically detects railway features such as rails, ties, and fasteners as well as defects such as cracking of concrete ties. Additionally, track geometry, gauge width, alignment, wear and a wide variety of other mechanical parameters can also be measured.  These same principles can also be applied to roads, bridges and other forms of infrastructure to survey cracks and other structural defects. In the images below (courtesy of Pavemetrics) you can see an example of how such a system could be deployed for both rail (left) and road (right) applications.
One ideal laser source for laser rail inspection is the FocusFlux EL laser series from Focuslight, a fiber coupled high powered diode laser system with a laser line beam shaper offered by us here at RPMC. The EL laser series, which was specifically designed for this type of application, is available with fan angles of  75-degree, 90-degree, and 110-degree, depending on the configuration requirements of your specific application. Each of these options provides >85% line uniformity with a total output power >20 watts.
In addition to obvious advantages of the micro-optic beam shaping technology discussed above, the EL series of lasers also provide you with high reliability and maintenance-free operation with laser lifetimes > 20,000 hours and a wide operating temperature range from -40o C to +70o C making them ideal for year-round operation even in the harshest of environments.
For detailed technical specifications on the FocusFlux EL laser series of high-power line-shaped laser diodes from Focuslight click here or talk to one of our laser experts today by calling 1-636-272-7227.