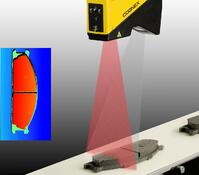
Machine vision can utilize a variety of schemes for image detection and analysis. Lighting can influence that analysis and lasers are often used to illuminate objects with structured illumination. This can be useful in providing additional information about the objects through image processing. Examples of information that can be obtained include defects, location, dimensions, dents, punctures, and alignment, for example.
Figure 1: Applications of lasers to machine vision.
Output Power
One of the first things a designer should know is how much optical power they need, and the corresponding classification of the laser at that power as determined by your respective regulatory agency. In the U.S., Class IIIa lasers are typically considered safe as their total collected radiant power collected by the eye is less than 5 mW. This means the optical power collected in a “7-mm-diameter circular aperture with a solid angle of acceptance of 10^-3 steradian with collimating optics of 5 diopters or less”.¹ Lasers exceeding the above optical power constraints, require the use of a controlled environment. Examples of higher power lasers include those used for medical, or material processing applications, where the risk of accidental eye exposure is controlled. You should always consult with a laser safety engineer prior to commercializing a product that uses lasers. For most systems that use visible cameras or photodetectors, 5 mW may actually be too much power, and attenuators may be incorporated into the system, or you may need to use an adjustable power supply. The system designer should try to characterize the system to determine the minimum and maximum optical power requirements. COMPLIANCE GUIDE FOR LASER PRODUCTS (https://www.fda.gov/media/74026/download) Laser optical power can vary over time due to power supply variations or aging of components. Does your system require power stability? If so, how much can be tolerated by your detection system? Some modules have feedback mechanisms to control power but might cost a little bit more. Power stability is often specified in terms of how much the power varies as a percentage of the typical or specified optical power. For example, over a 24-hour period, the power might be specified as <0.5%, and over the lifetime of the laser the stability might be <3.0%. If you need more or less stability, be sure to let your vendor know, but keep in mind that extreme specs may command a premium.Wavelengths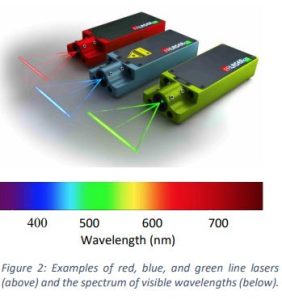
Typically, visible-wavelength lasers are used for machine vision systems, as cameras and detectors are readily available, and the beams are easier to align. Some circumstances can dictate the use of infrared or even ultraviolet lasers. The most common visible wavelengths include blue, green, and red. Wavelengths are expressed in units of nanometers (nm). Some of the most common colors and their wavelength ranges are blue (405-450 nm), green (532-550 nm), red (635-680 nm), as shown in Figure 2. In the near infrared portion of the spectrum, typical wavelengths that are used are: 830, 980, 1060, and 1550nm, but you can get many wavelengths in between. Try to understand if wavelength matters for your application, as some wavelengths are less expensive and others are available in higher power. If you need a green laser, but the exact wavelength doesn’t matter, let your vendor know you have a wide tolerance. An example of how you might spec this is: 540 ± 10 nm.
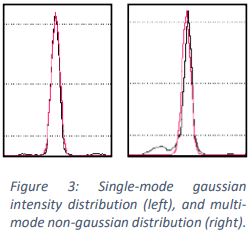